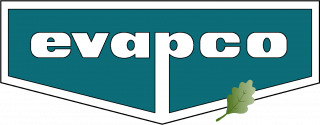
Adiabatic Dry Coolers
Features & Benefits
Dry coolers products with adiabatic cooling pads, are designed to permit the most flexible, economical and hygenically safe cooling system available today.
The product allows for cost effective dry cooling during applicable temperatures combined with economic precooling of the entering air to achieve operating temperatures similar to evaporative equipment.
The control sequence is designed to enable the unit to adjust accordingly to achieve the lowest energy and water use as ambient conditions change.
Control Options
EAS offers a wide range of control option for different setups.
- Basic - EC enclosures
- Premium - EC enclosures
- Basic Controller ir33
- Premium Controller pCO5
- F-Controller
- U-Controller
- Safety Switch
- Common Terminal
Details of each option can be found HERE or in the Control options section in the top menu.
Options & Accessories
Casing Material options
- AluZinc –185
- Aluminium Magnesium
- 304 AISI
- 316 AISI
Coil Tubes and Headers
- Copper
- Aluminium
- 304 AISI
- 316 AISI
- Titanium
Fins
- Aluminium
- Copper
- Electro-Tinned Copper (CuSn)
- Aluminium Magnesium (AlMg)
- Pre-Coated Aluminium (AlEp)
- Hydrophilic (AlHy)
Optional Accessories / Maximum Performance.
- EC - Electronically Commutated Motors.
- Factory Programmed Controls.
- Adiabatic spray system ~ FlexSpray.
- Customizable dimensions.
- Customizable controls.
- Multiple and optimized fan selections.
FlexSpray Dry Coolers
Features & benefits
The FlexSpray Cooling option can be added to single and double coil arrangements. The FlexSpray package is available in various combinations to suit your needs. The system can be fully integrated with step controls or a simple spray system to be controlled manually or by your choice. Existing units either Flex coil or competitors models can also be fitted with the FlexSpray system.
Basic operation, on a fully controlled unit, energizes the electromechanical valve system as the final step in the control sequence to reach the leaving water or refrigerant set point. With a VFD system, once all motors have reached full speed and the set point is not met with air only, the electromechanical valves energize and the spray comes on. The dead band range prevents the valve body from oscillating on and off and allows the spray to run to minimize thermal shocking. Using step control, the electromechanical valve system will energize after the last motor is energized and the set point triggers the valve to open.